Co-extruded Wood Profiles With Elastic Surface
At present, in the field of decoration, indoor deck paving materials are generally various wooden decks or composite wooden decks. Wooden decking feels relatively comfortable under the feet, but problems such as expansion, deformation, warping and cracking often occur during use.Plastic wood decking is a new type of environmentally friendly plastic wood composite product.It is mainly composed of wood powder, plant fiber, thermoplastic polymer materials and processing aids.It is a high-tech green environmentally friendly material that is mixed evenly and then heated and extruded by mold equipment. It has the properties and characteristics of wood and plastic, and can be a new environmentally friendly high-tech material that can replace wood and plastic.
With the development of the times, the demand for some special decks is also increasing, such as basketball court decks. Basketball court decks are required to have good anti-slip properties and buffering properties. However, the existing plastic wood decks have poor elasticity and adhesion properties, and are prone to aging, cracking and wear. If the surface is too soft, although it has good resilience, the hardness often does not meet the actual requirements, which will lead to poor foot feel, easy wear, and aging.Elastic surface co-extruded wood profile and its preparation method, that is, the design of the double-layer elastic layer of the co-extruded wood profile,It ensures that co-extruded wood profiles have high resilience, wear resistance and oxidation resistance, and their service life is significantly extended.Elastic surface co-extruded wood profiles, including core material layer, elastic inner layer and elastic surface layer,By weight, the elastic inner layer includes the following raw materials by weight:20-30 parts of natural rubber, 15-20 parts of polypropylene oxide ether polyol, 15-20 parts of high-density polyethylene, 20-25 parts of poplar wood powder,3-8 parts of coupling agent,2-5 parts of compatibilizer, 3-5 parts of plasticizer, 5-8 parts of calcium carbonate,The elastic surface layer includes the following raw materials by weight: 20-30 parts of high-density polyethylene, 20-25 parts of poplar wood powder, 10-15 parts of elastic material, 3-6 parts of compatibilizer, 3-5 parts of coupling agent, 2‑3 parts of antioxidant, 1‑2 parts of anti-UV agent, 2‑4 parts of calcium carbonate. The thickness of the elastic surface layer is about 1/2 of the elastic inner layer.
The effect: First, two outer layers are hot-pressed outside the core material layer. The elastic inner layer is relatively soft and highly elastic, while the hardness of the elastic surface layer is higher than that of the elastic inner layer.But it is softer than the core material layer and has better wear resistance. The elastic inner layer ensures the overall high elasticity of the co-extruded wood profile.At the same time, it also acts as a buffer against damage to the core material caused by strong impact on the elastic surface layer.Secondly, natural rubber has good resilience, strong buffering capacity, and is not easy to deform after forming rubber, while polypropylene oxide ether polyol has good elastic properties, making the elastic inner layer highly elastic.And because it is protected by the outer layer, it is not easy to oxidize, has high thermal stability, and is more environmentally friendly;A certain amount of elastic material is added to the elastic surface layer, so that the surface layer has a certain degree of resilience, and the resilience can meet the usage requirements.The content of high-density polyethylene is higher than that of the elastic inner layer to ensure its wear resistance. At the same time, antioxidants and anti-UV agents are added to ensure the antioxidant capacity of the surface layer and prevent UV damage.
Relatest Post
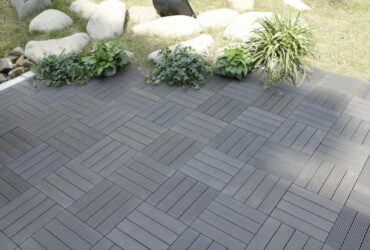
Wood Plastic Composite Material Flame Retardant Heat Insulation Technology Solution
Details icon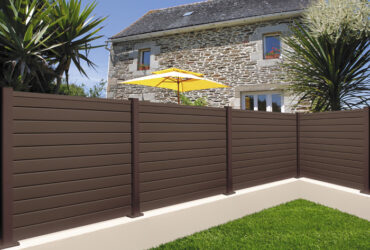
What Are The Advantages Of Plastic Wood Fence In The Decoration Industry?
Details icon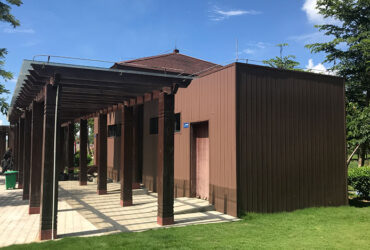